
Basic knowledge of copper terminals: open the door of electrical connection
In modern electronic engineering, copper terminals play an indispensable role. It is not only a bridge between wires and electrical components, but also an important guarantee to ensure the smooth transmission of current. So, what exactly is a copper terminal? Simply put, a copper terminal is a small part used to fix the end of a cable and connect it to another conductor. It is usually made of high-purity copper, which has good electrical conductivity and mechanical strength.
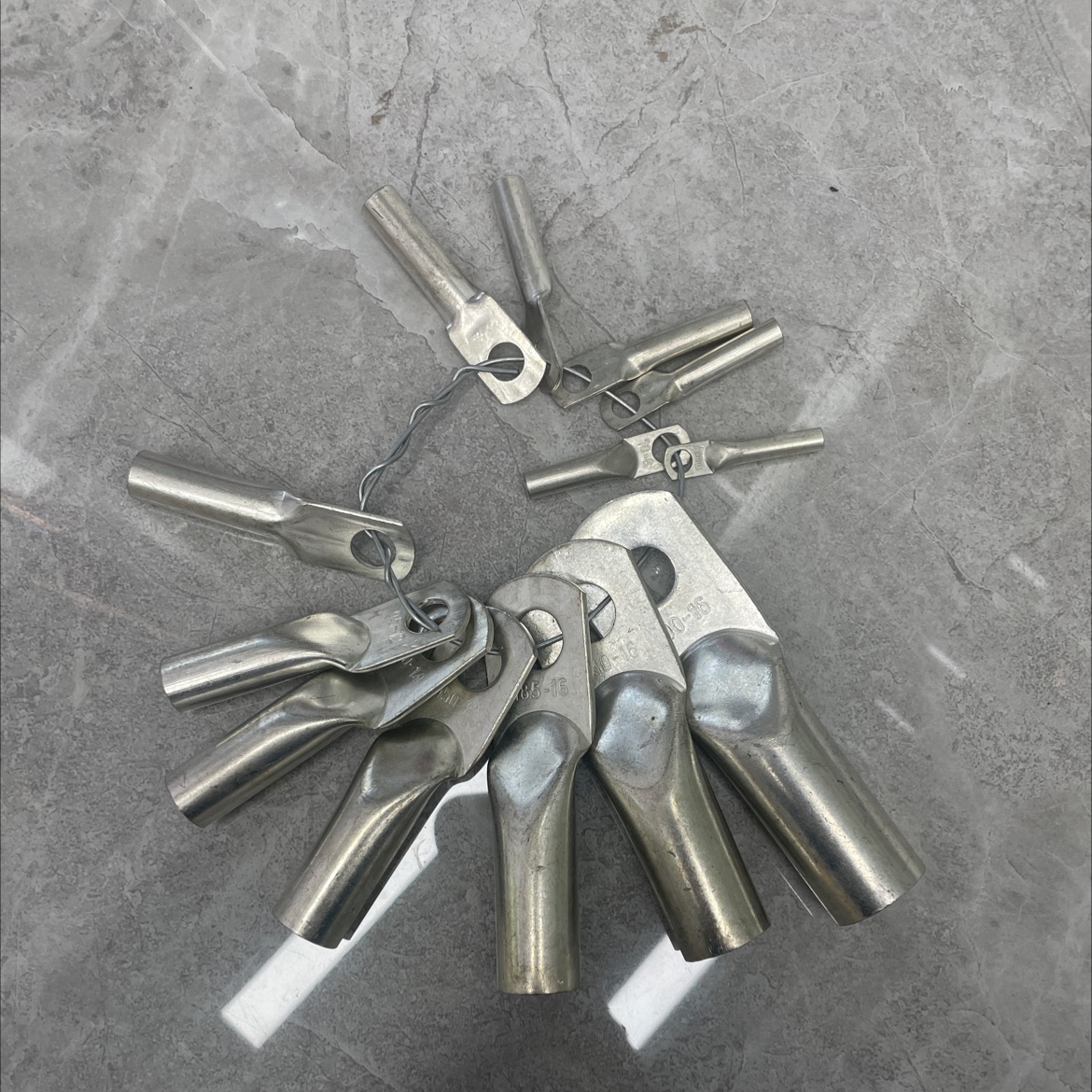
From a historical point of view, copper, as one of the earliest metals used by humans, has been used in simple tool making in ancient times. With the development of time, people's demand for electricity is increasing, and copper has gradually become the preferred material because of its excellent physical properties. Nowadays, whether it is household electricity or complex industrial control systems, copper terminals can be seen almost everywhere.
Why choose copper? Uncover the charm of the king of metals
Compared with other common conductor materials, such as aluminum, copper has unparalleled advantages. First of all, copper has strong corrosion resistance. This means that even if it is exposed to moisture for a long time, it is not easy to rust and damage, ensuring long-term stability. Second, copper has excellent thermal conductivity. When the temperature rises, the heat can be quickly dissipated to prevent overheating and improve the overall safety factor.
In addition, the lower resistance value is also a highlight of copper. Lower resistance means higher energy transfer efficiency, reducing energy waste and reducing heat generation hazards. These properties make copper the most popular choice in many fields. For example, in large data centers, a large number of high-quality copper terminals are used in the power distribution cabinets in the server room to meet the requirements of continuous and stable power supply.
Different types of copper terminals and their application scenarios
There are many different forms of copper terminal products on the market. One of the most typical is the bolt type, insert type and welding type distinction method:
- Bolt-type copper terminals: are commonly found inside high-voltage switchgear in power transmission systems. Solid and reliable electrical connection is realized by tightening screws, which is suitable for frequent disassembly and maintenance.
- Blade copper terminals: Mainly used for compact wiring between electric vehicle battery packs. The compact and lightweight design is easy to insert and pull out quickly, which greatly facilitates production and maintenance operations.
- Soldered copper terminals: are more common in permanent fixed installation locations, such as outdoor lighting facilities or temporary power distribution boxes on construction sites. With strong and durable features by the engineers of all ages.
Different scenarios determine the unique value of various types of copper terminals. In any industry, choosing the right model for your project is a crucial step.
Proper installation and maintenance of copper terminals: ensuring long-term reliability
To give full play to the role of copper terminals, correct installation and regular maintenance are essential. When purchasing, pay attention to whether the size and specification match the equipment requirements, and give priority to the qualified certification products provided by well-known brands. In addition, in the actual operation process, it is necessary to strictly follow the relevant manual guidelines, so as to avoid failure or even safety accidents caused by misoperation.
during daily use, we should also pay attention to some key details, such as regular inspection of each part for signs of loosening, and re-reinforcement if necessary; timely cleaning of dust and oil accumulated on the surface to avoid oxidation reaction affecting contact quality, etc. As long as scientific and reasonable management and maintenance, can greatly extend the service life and always maintain the best condition.
Innovation and Development: Copper Terminal Solutions for Future Trends
With the rapid development of science and technology, a new generation of high-performance copper terminals is quietly rising. The research and development of new materials has injected fresh vitality into the traditional process. The new alloy materials not only retain the original excellent characteristics, but also achieve breakthrough improvements in some aspects. At the same time, the application of intelligent sensing technology also brings a new experience for remote monitoring and management. The built-in chip of the sensor can automatically alarm in abnormal situations, helping technicians to take measures to solve the problem in the first time.
Especially in the context of the rapid development of the new energy vehicle industry, higher-level standards have been proposed for special designs under specific environmental conditions. In addition to the regular level of protection, waterproof, dustproof and anti-vibration functions have also become important indicators to measure the pros and cons. It is expected that more personalized customized services will emerge in the next few years to meet the needs of diversified markets.
Successful Case Analysis: Copper Terminal Helps Industrial Upgrading
Many enterprises and engineering projects have achieved remarkable results with the help of efficient and stable copper terminals. A well-known communications operator has built a number of high-speed broadband network node stations across the country. Due to the selection of top-brand copper terminal products, it has effectively solved the problem of serious signal attenuation in the past and greatly improved the level of service quality. Statistics show that the customer complaint rate has dropped by more than 30%.
Let's look at a company focused on clean energy power generation. They introduced a new DC bus system on the top of the wind turbine tower, all assembled with special reinforced copper terminals. In this way, not only the bearing capacity and heat dissipation efficiency of the system are enhanced, but also the difficulty of on-site construction is simplified. After a period of actual operation inspection, the cost per kilowatt hour has been significantly reduced, creating considerable economic and social benefits for the enterprise.
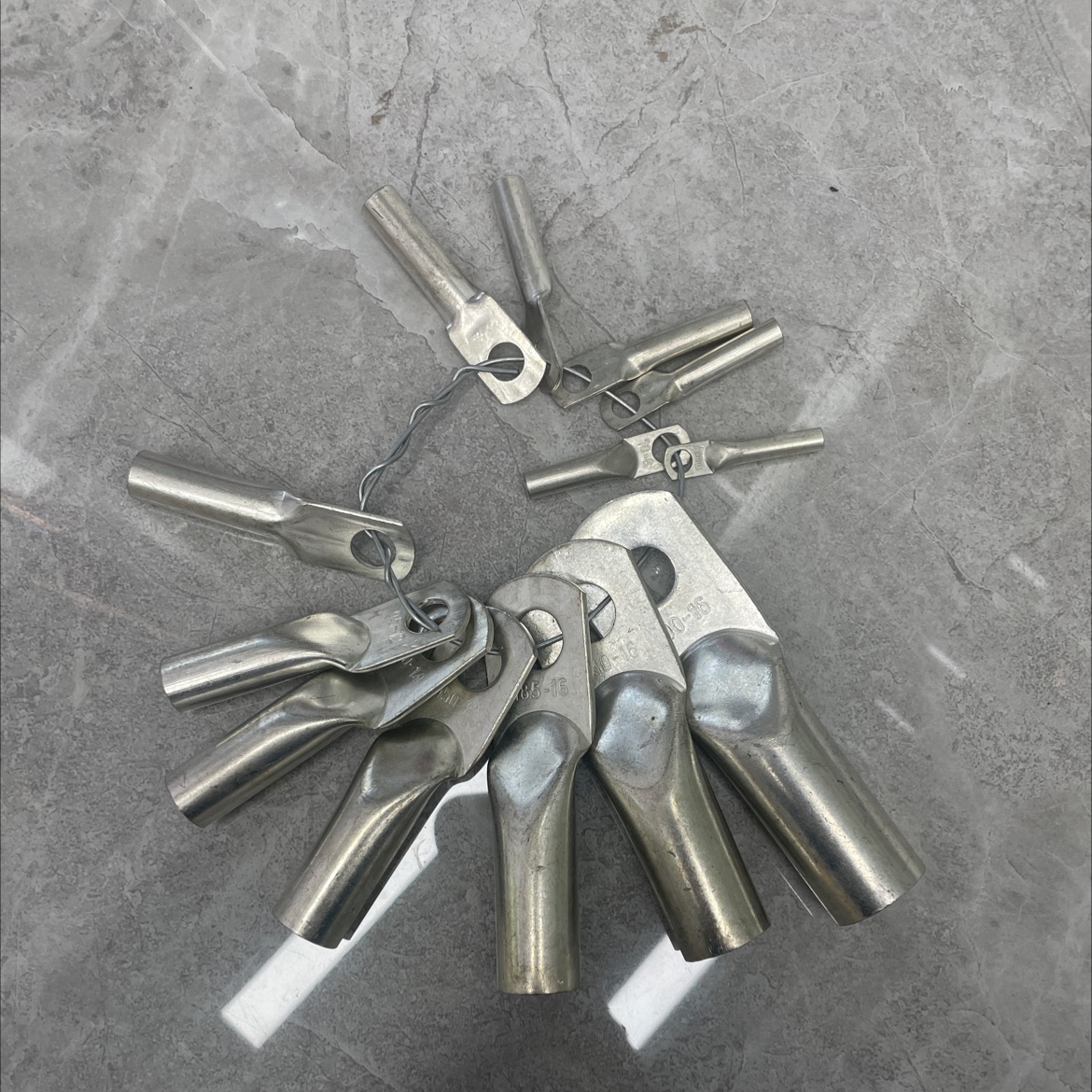